3D-printed Bearings:
Less material = less weight
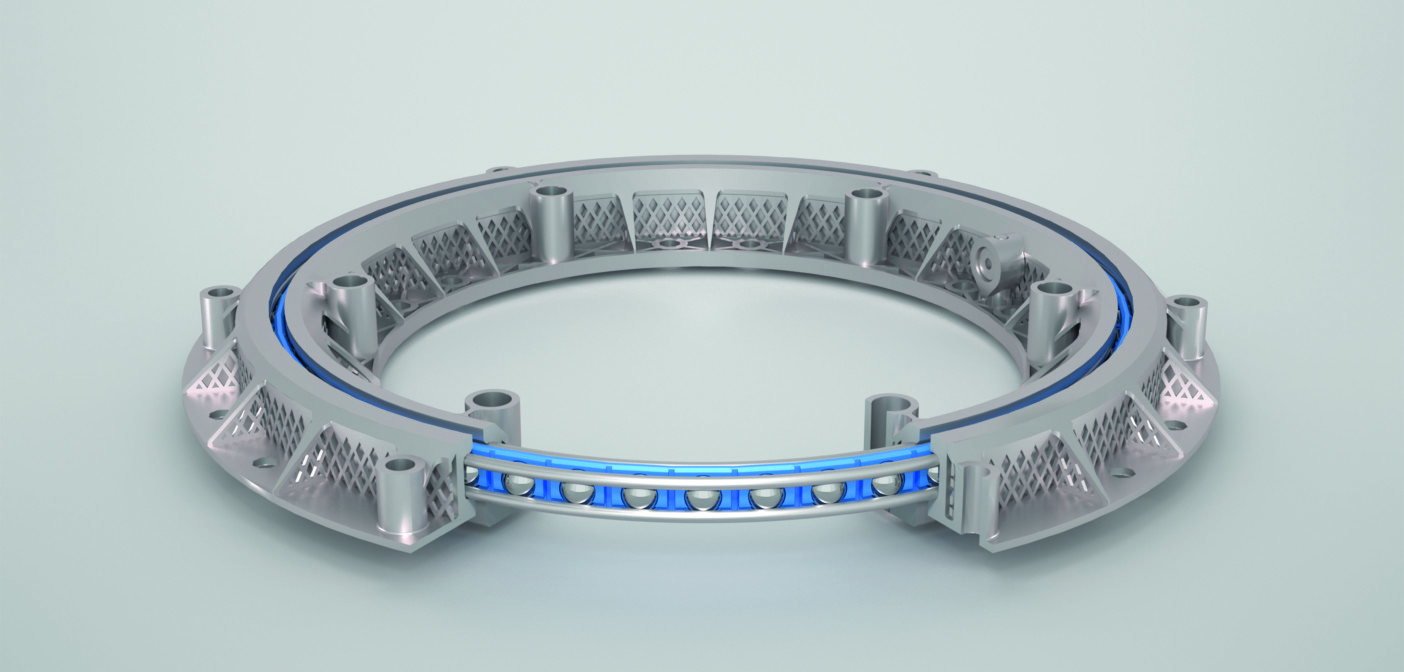
Lightweight bearings with housing parts printed in 3D combine high load capacity and light weight.
Aluminum, plastic, carbon – lightweight bearing assemblies with integrated wire race bearings have been successfully implemented in many different combinations of materials. Now it goes to alternative manufacturing processes for the production of the housing parts. Laser sintered aluminum rings from 3D printers are currently state of the art. This method makes it possible to create a kind of honeycomb structure inside the housing parts, which makes the ring, at the same time, light and stiff.
Currently a prototype is tested and an entire bearing is constructed. Extensive tests will show at the end, how the lightweight bearing from the printer will perform in terms of load and precision when compared to conventionally produced aluminum bearings.
Expert Interview: 3D printing opens up new possibilities for designers.
Franz Öhlert from the Franke R&D department talks about the construction of lightweight bearings and about the new technology of 3D printing.
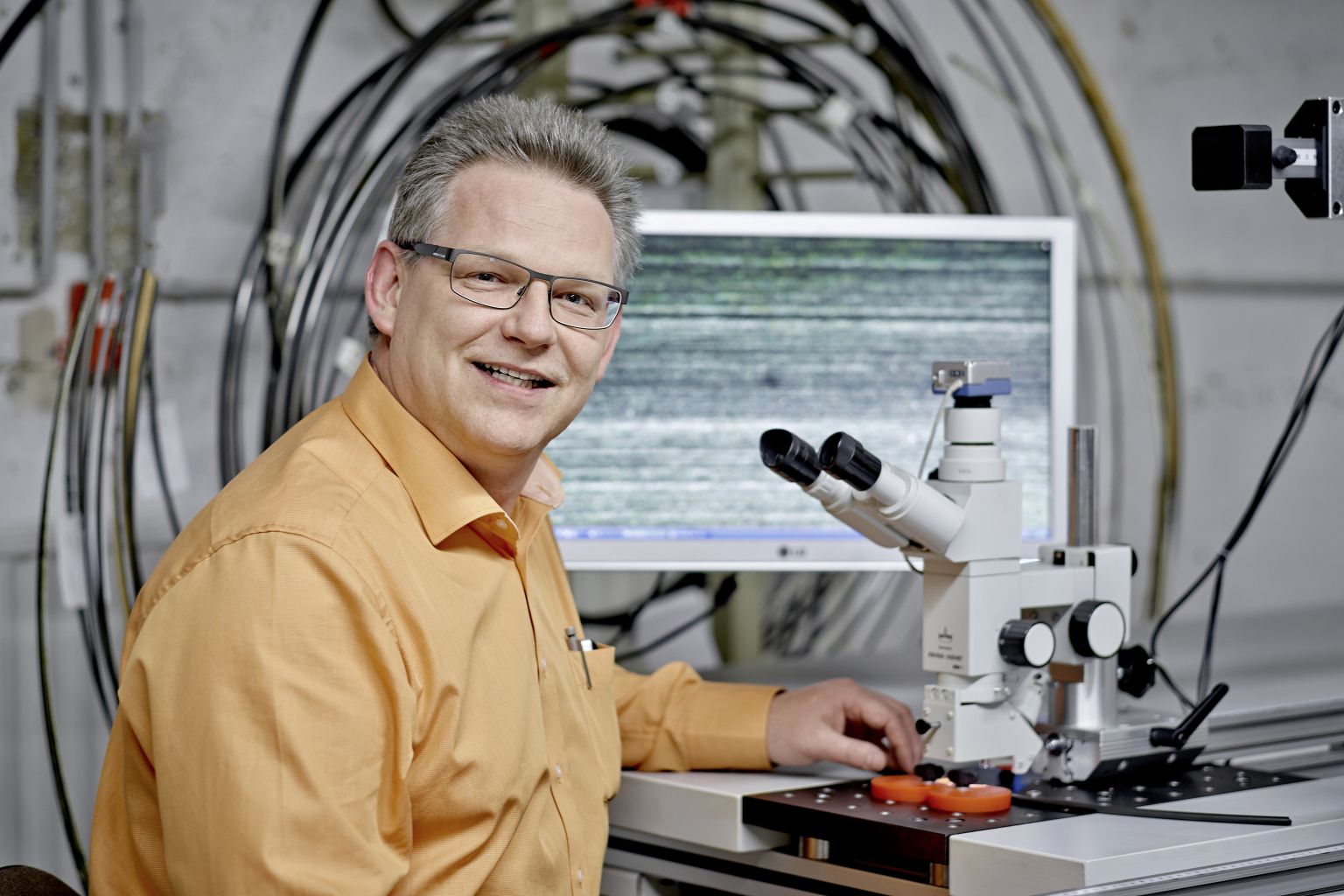
Franz Öhlert is the Franke specialist for bearing development.
Mr. Oehlert, what 3D printing really mean?
Franz Öhlert: In principle, it stands for production processes in which objects are built up in layers of particles. This is called additive process. This represents a reversal of conventional methods which are associated in general with the removal of material, for example in the form of chips.
Do you have a particular method in mind when it comes to the construction of bearing assemblies?
Franz Öhlert: We are currently focusing on the so-called laser sintering. This produces workpieces of metal or plastics. In our view, the laser sintering is one of the most promising options in the field of additive processes.
How does this work?
Franz Öhlert: As the name suggests, in laser sintering a high-energy laser beam is used. It heats the metal powder at defined points up to the melting point. Once a thin layer of powder is processed, the work piece is lowered, new powder is spread out and merged again selectively. This way the work piece is created layer by layer. In the end, the cooled mold is removed and the rest of the material can be used for other workpieces.
Why is Franke interested in 3D printing processes?
Franz Öhlert: We are constantly searching for innovative technologies that enable us to design to the needs of our customers. Lightweight construction is currently on everybodies lips. 3D printing has a lot to offer in this regard.
What has 3D printing to do with lightweight?
Franz Öhlert: The core competence of lightweight design is the ability to omit material wherever it is not needed. Traditional lightweight bearings of Franke start at precisely this. Through elaborate investigation and analysis, we are able to design the mating structure of our wire race bearings in such a way that material and thicknesses meet the load situation of the application. The choice of the material – often aluminum – is taken into account. However, we are limited in defining the geometry of the parts. Not everything that looks good on the CAD screen can be realized. Restrictions of manufacturing technology and economics get in the way often. The parts must be able to be machined and their production must be profitable in the end.
3D printing shuffles the cards again. The layered structure of the parts gives us completely new possibilities in design. Internal honeycomb structures, varying wall thicknesses and even a mix of materials are possible.
Does the capacity of the bearing suffer from that?
Franz Öhlert: No. Here the ingenious principle of Franke wire race bearings come to effect. The performance of the bearing is influenced only to a small part by the enclosing structure. All loads are initially absorbed by the raceways of the bearing wires. Certainly, these races require a corresponding raceway bed. But texture and material of the mating structure can be freely selected. Wire-race bearings are thus ideally suited for 3D components.
Where do you see possibilities for 3D printed bearings?
Franz Öhlert: We are still at the very beginning to experiment with this new technology. The first attempts, however, are promising. we see applications wherever weight is critical, driving energy has to be saved or special material is needed. Target sectors could be aerospace, automotive industry or medical technology. Also HRC-robots for small and easy assistance of human tasks can benefit from 3-D-printed lightweight bearings.
CROSS ROLLER BEARINGS
Cross Roller Bearings for higher load capacity [...]
LIGHTWEIGHT BEARINGS FROM 3D-PRINTING
Lightweight Bearings from 3D-printing: New chances for designers and [...]
FRANKE INNOVATIV MAGAZINE ISSUE 8
ISSUE 8 FRANKE INNOVATIV MAGAZINE AVAILABLE NOW The [...]
SLIM BEARINGS DAMPEN RUNNING NOISE
Franke Slim Bearings dampen running noise Franke [...]