Lightweight Bearings from 3D-printing: New chances for designers and manufacturers
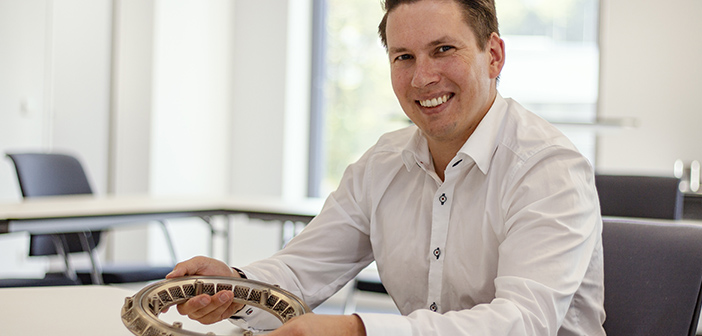
3D printing opens up completely new possibilities for designers. Philipp Engert from the Technical Sales Department talks in an expert interview about how the new technology can be used to build lightweight bearings. And about the benefit of this technology.
Mr. Engert, what is 3D-printing all about?
Philipp Engert: In principle, this means production processes in which objects are built up in layers of small particles. We also call it “additive procedure”.
Do you have a specific procedure for the application at Franke?
Philipp Engert: We are currently concentrating on so-called laser sintering. This creates
workpieces made of metal or plastic. From our point of view, laser sintering is one of the most
promising variants in the field of additive processing.
How does this work?
Philipp Engert: As the name implies, laser sintering uses a high-energy laser beam. He heats the metal powder at defined points and melts it together. The following article illustrates the principle in detail: https://www.franke-innovativ.de/en/3d-printed-bearing-rings/
Why is Franke interested in 3D-printing?
Philipp Engert: We are always on the lookout for innovative technologies that enable us to
meet the demands of our customers. Lightweight construction is currently on everyone‘s lips across all industries. 3D printing has a lot to offer in this respect.
What has 3D-printing to do with lightweight?
Philipp Engert: Perfect lightweight construction is the ability to omit material wherever it is not
needed. 3D printing gives us completely new ways to design parts geometries. The adaptation
of the housing parts to the enclosing construction can also be done almost seamlessly.
Is there a risk that this might lead to a weakness of the bearing concerning the load capacity?
Philipp Engert: No. This is where the ingenious principle of the Franke Wire Race Bearings
enters the game. The performance of the bearing is only partially influenced by the enclosing structure. All loads are initially absorbed by the races of the wire race bearings. Certainly, these races need a corresponding ring bed. But the nature and material of the enclosing construction are freely selectable. Wire race bearings are therefore ideally suited for 3D components.
Where do you see applications for 3D printed bearing assemblies?
Philipp Engert: Applications are interesting as soon as the following parameters are required:
• lowest weight,
• bespoke design,
• smallest installation space and
• fast availability even with batch size 1.
For example, service robots, which are designed to be small and lightweight and designed to relieve
people of their jobs, can benefit from 3D printed lightweight bearings, as well as aerospace or light
electric vehicles.
FAQ’S DIRECT DRIVE
EVERYTHING YOU NEED TO KNOW ABOUT FRANKE DIRECT DRIVE [...]
BUILD YOUR OWN DIRECT DRIVE
BUILD YOUR OWN DIRECT DRIVE BEARING CAMPAIGN IS NOW LIVE! [...]
UK’S FIRST DIRECT DRIVE
FRANKE DIRECT DRIVE BEARING The UK's first Direct [...]
MOTION CONTROL
LIGHTWEIGHT BEARINGS FOR MOTION CONTROL Looking to take your motion [...]